Pushing The Boundaries of What’s Possible For Printable Materials
Across a wide range of materials, Bambu Lab filaments exhibit less ability to withstand mechanical load at elevated temperatures. These materials are less useful in real-world applications because of their reduced temperature performance. If you intend to use the output of your 3D printer in real-world applications, you should factor this into your purchase decision.
Putting Filaments to The Test
Our team held an experiment that simulated a printed part under a light load to mimic prolonged exposure to high temperatures like those found inside a car cabin or in a hot, outdoor environment. To explore material differences, we:
- Printed dogbone samples from various materials. Each sample measured 4mm high x 6mm wide x 100mm long, including radii at the ends.
- Placed the samples in an industrial oven similar to the Quincy Lab Model 40 with a 13-gram weight in the center and supported at both ends.
- Gradually increased the oven temperature, holding for 30 minutes every 3-5 degrees.
- Stopped the test when we observed over 5mm of sag in the sample
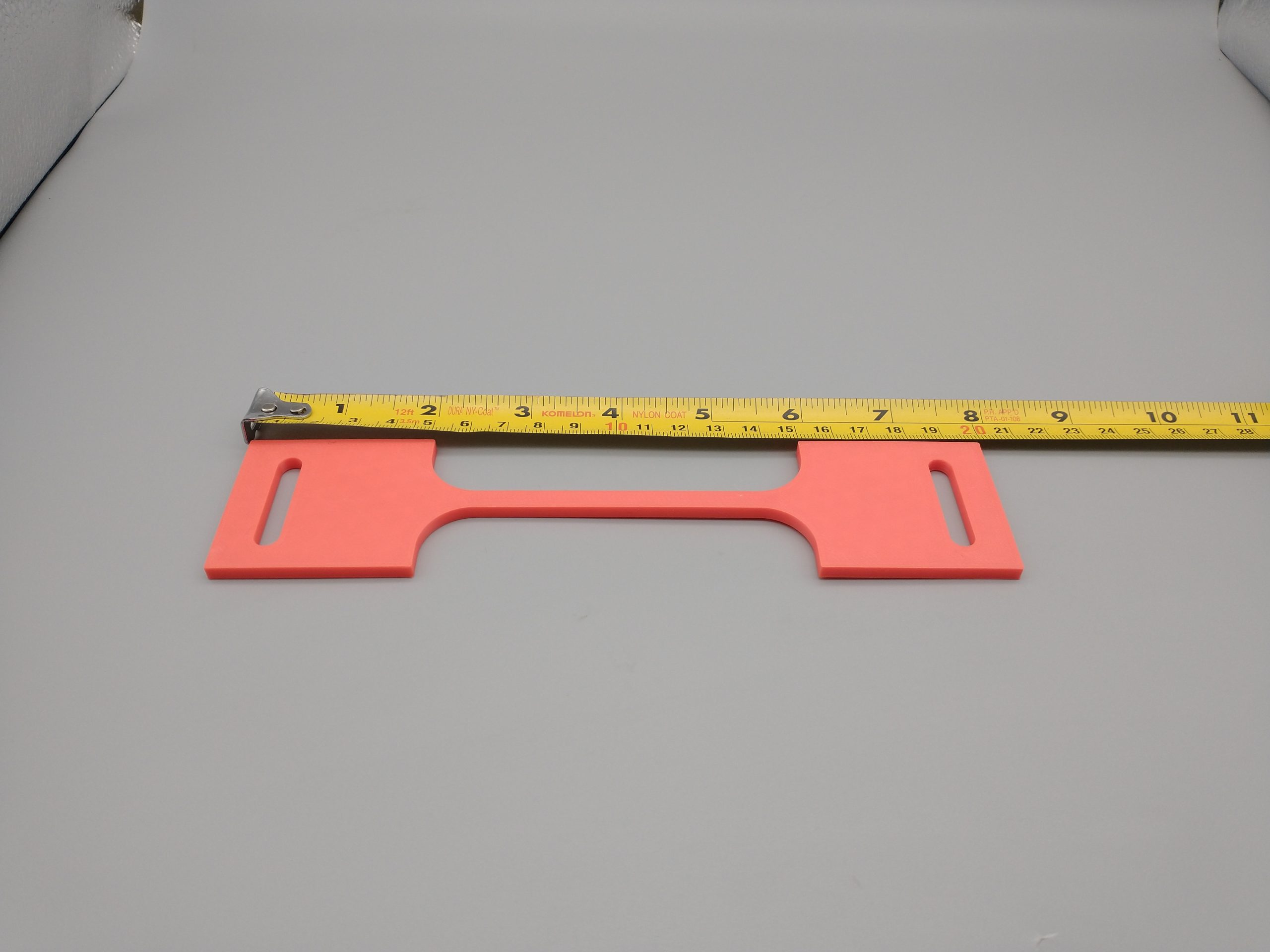
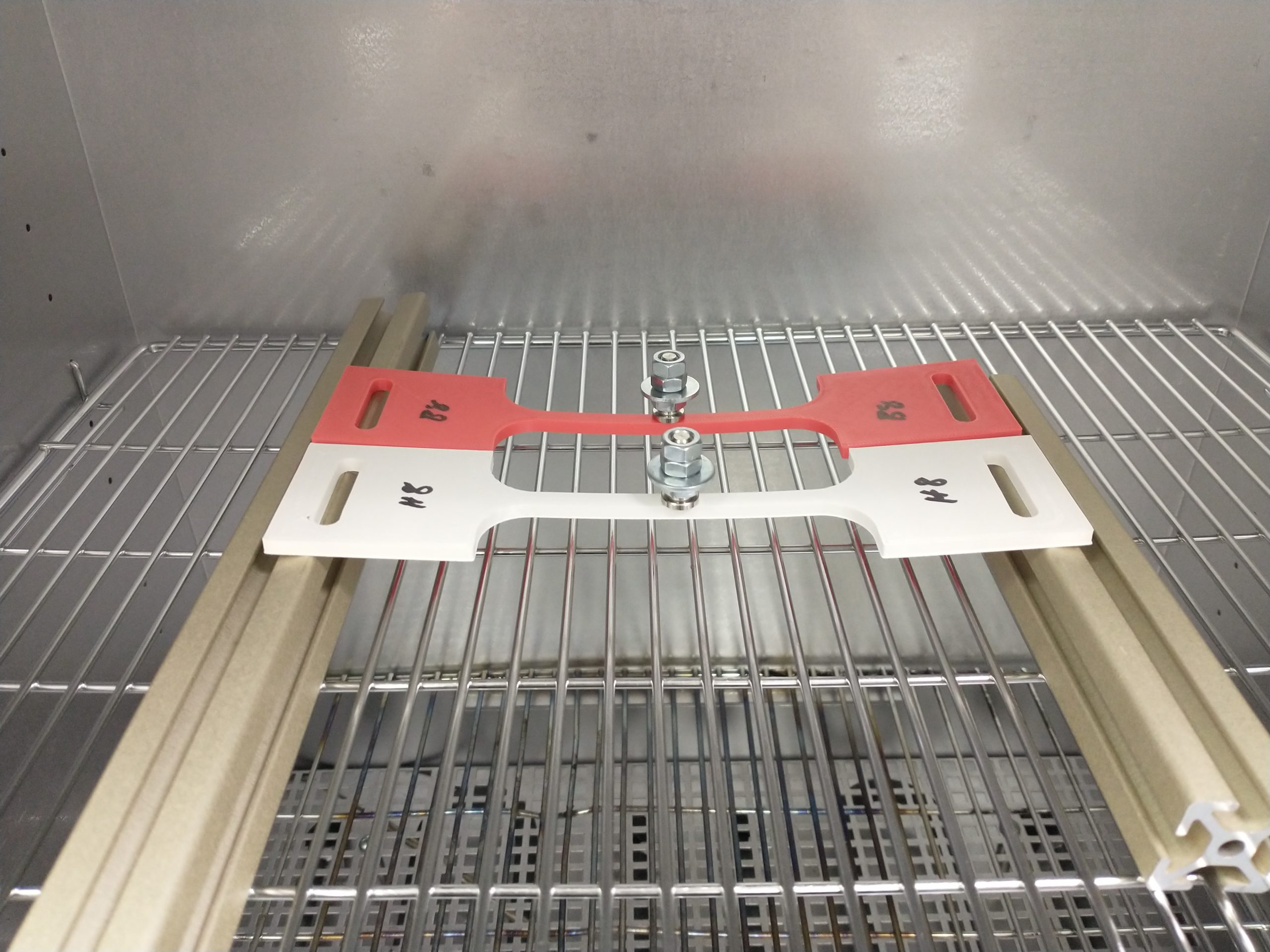
Our Findings
Our results clearly show that modifers used to enhance material printability have significant, negative impacts on temperature performance.
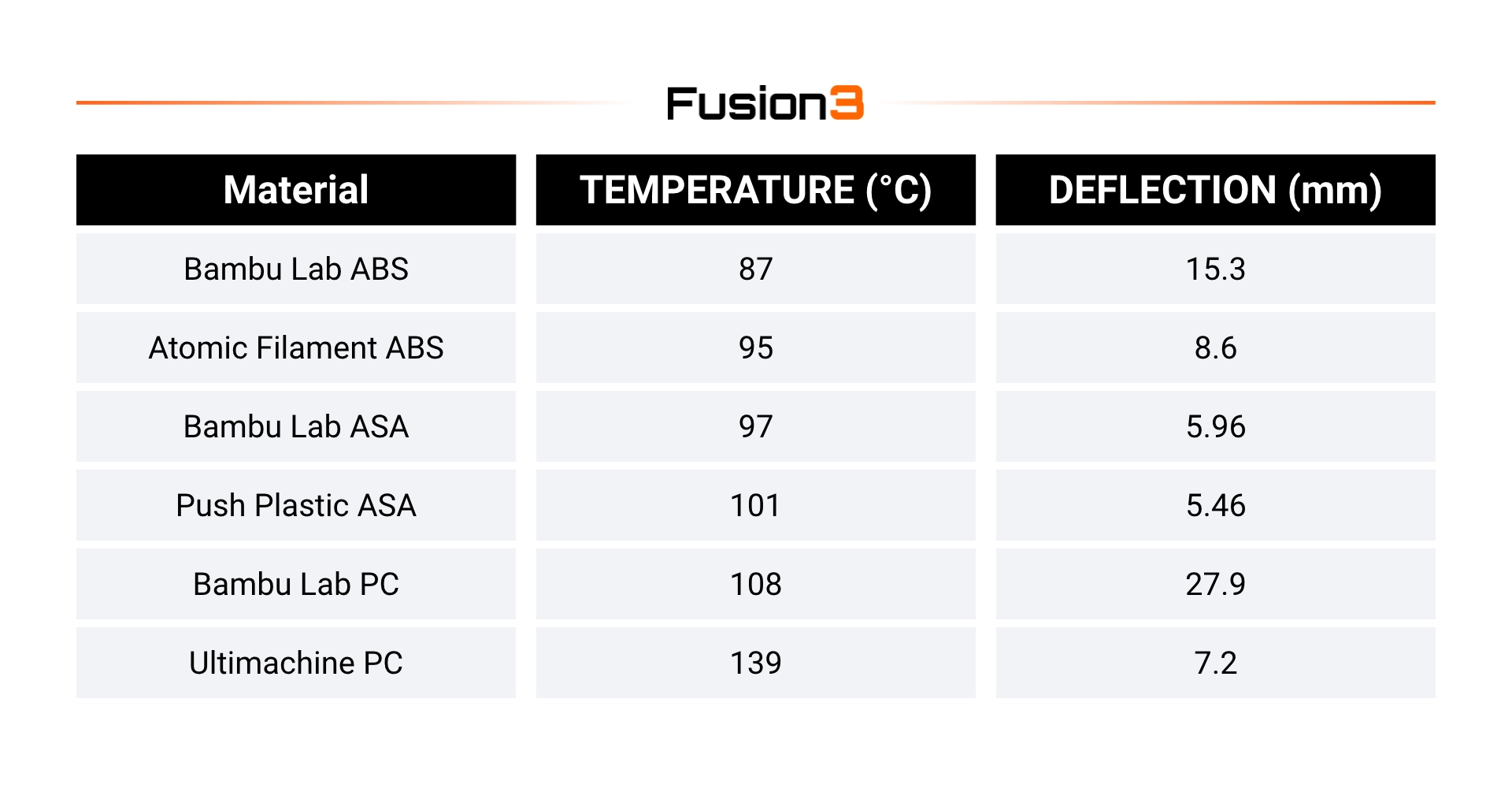
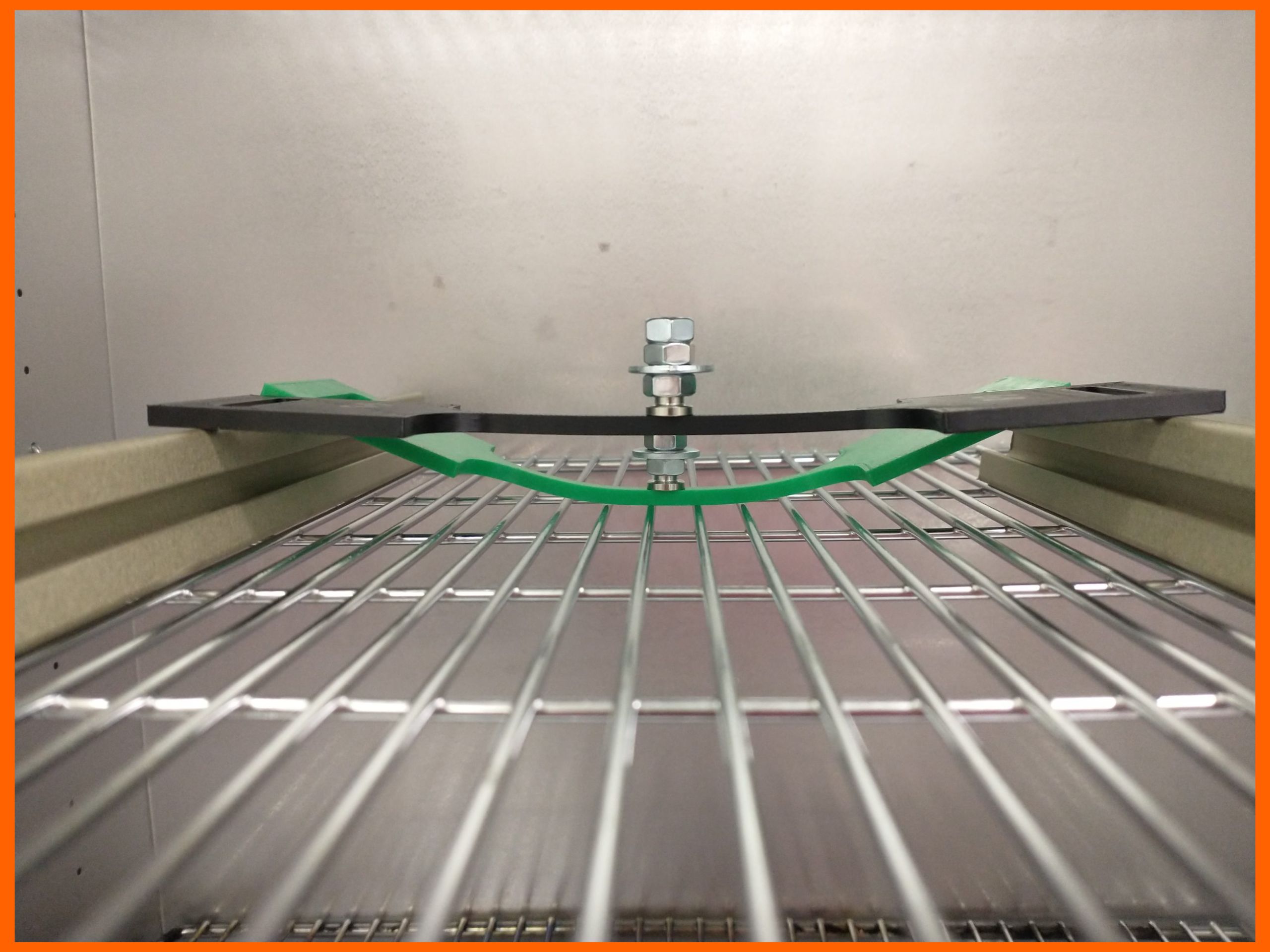
Atomic & Bambu ABS held at 95°C for 30 min
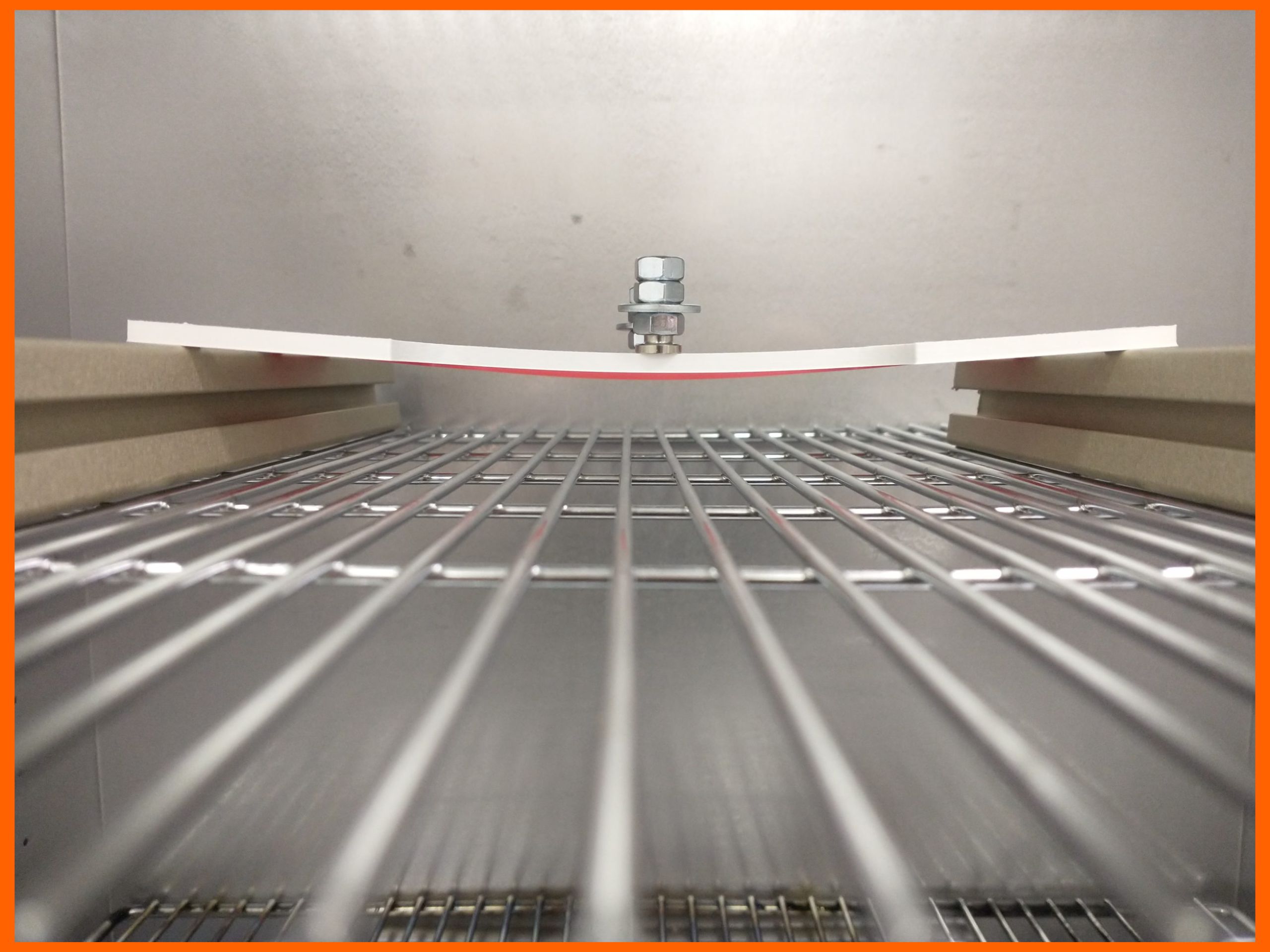
Atomic & Bambu ASA held at 97°C for 30 min
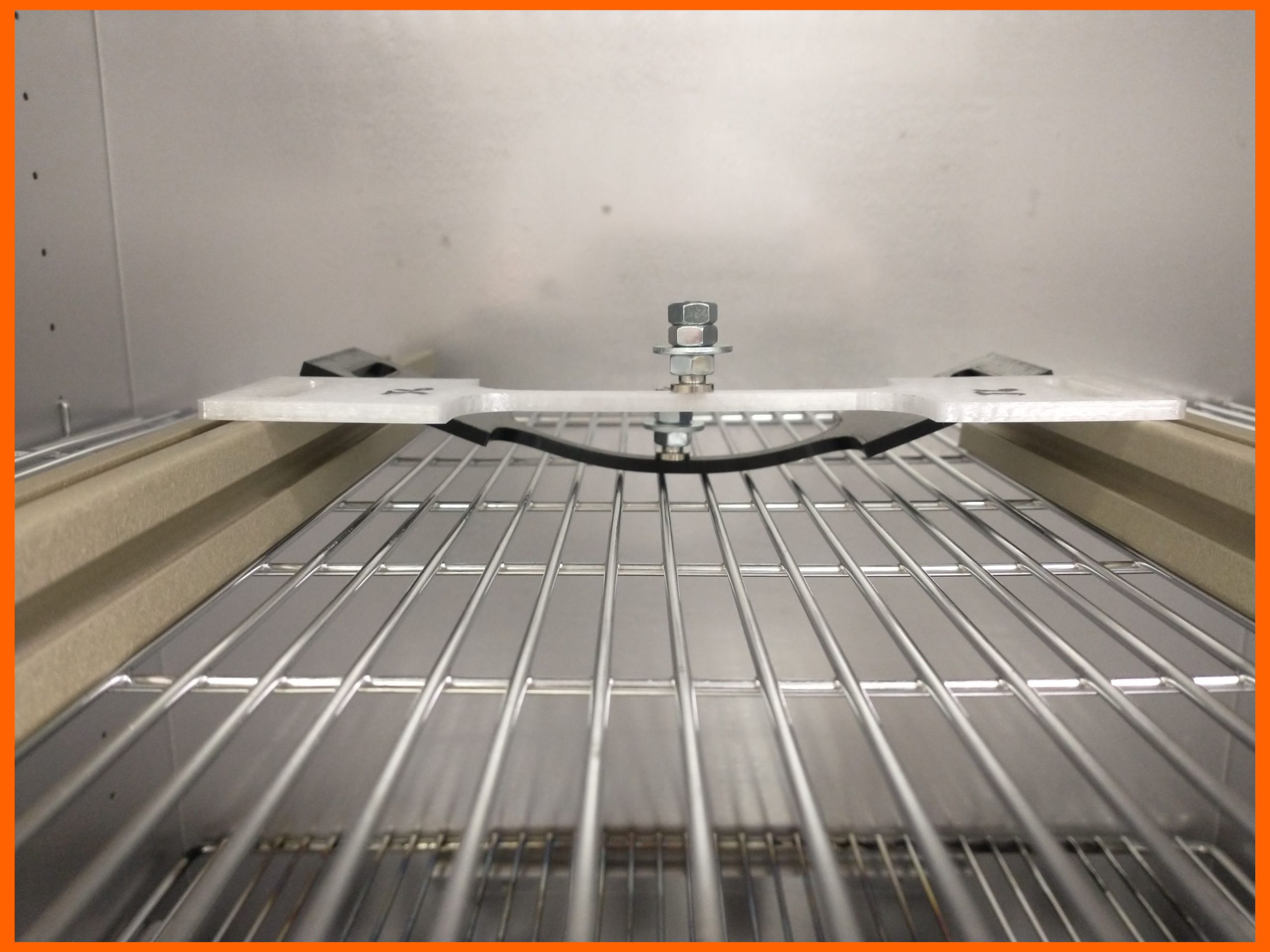
Atomic & Bambu PC held at 108°C for 30 min
Bambu ABS failed 8°C earlier than Atomic’s ABS
Bambu ASA failed 4°C earlier than Push Plastics’s ASA
Bambu PC failed over 31°C earlier than Ultimachine PC
Our Competitors Can’t Print Without Modifiers
Despite the manufacturer’s claims, materials lacking special modifiers printed poorly – or not at all – in Bambu Lab printers.
Case Study 1: Atomic ABS Electronics Housing
We printed an electronics housing on the Bambu Lab X1C with the same material we use on Fusion3 3D printers.
Specifications:
- Part Size: 223mm x 114mm x 68mm
- Wall Thickness: 3-2.5mm
- Material Used: 77g
- Print Settings: Bambu Studio generic ABS defaults
- Print Surface: Bambu Engineering Plate with purple glue stick coating
The thin-walled part exhibited so much shrinkage that it caused the build plate to detach from the magnetic base. The part remained adhered to the print surface but was so warped after removal that it became unusable. Plus, weak layer bonding made the part extremely fragile.
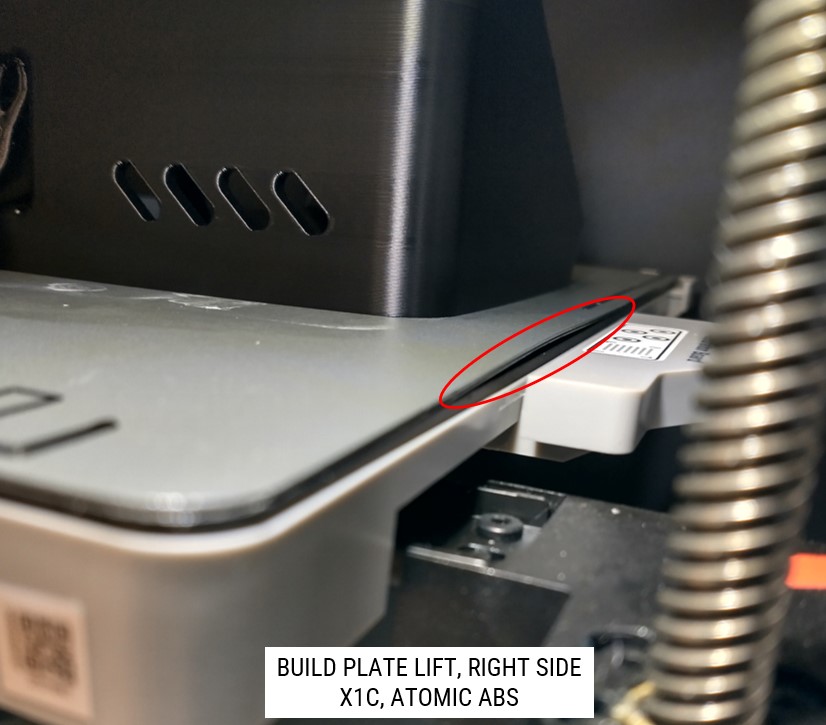
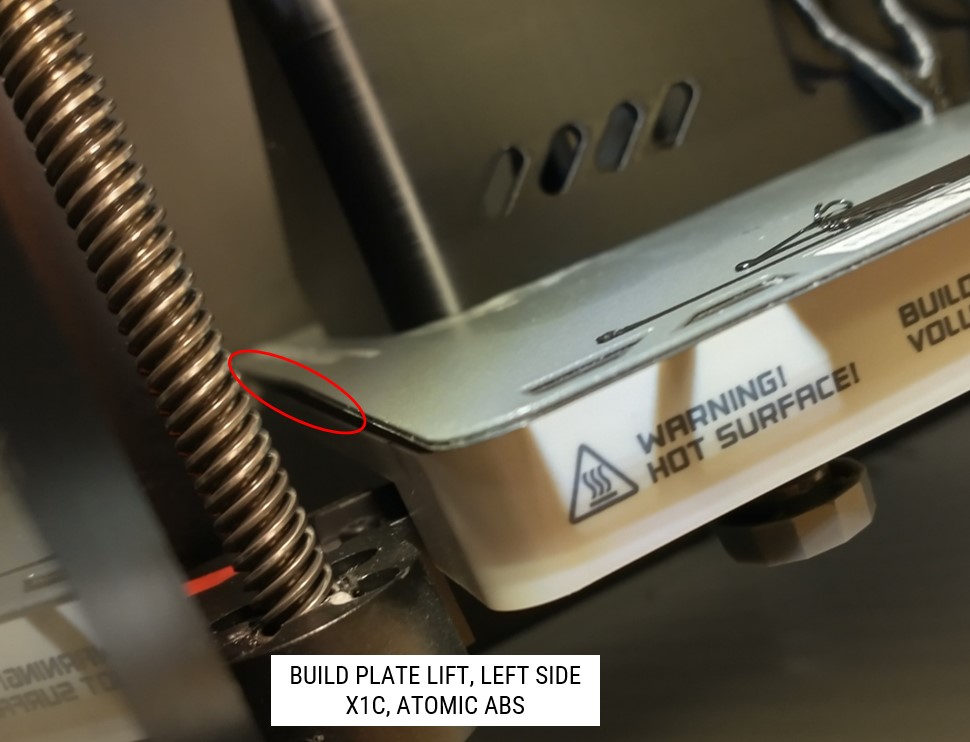
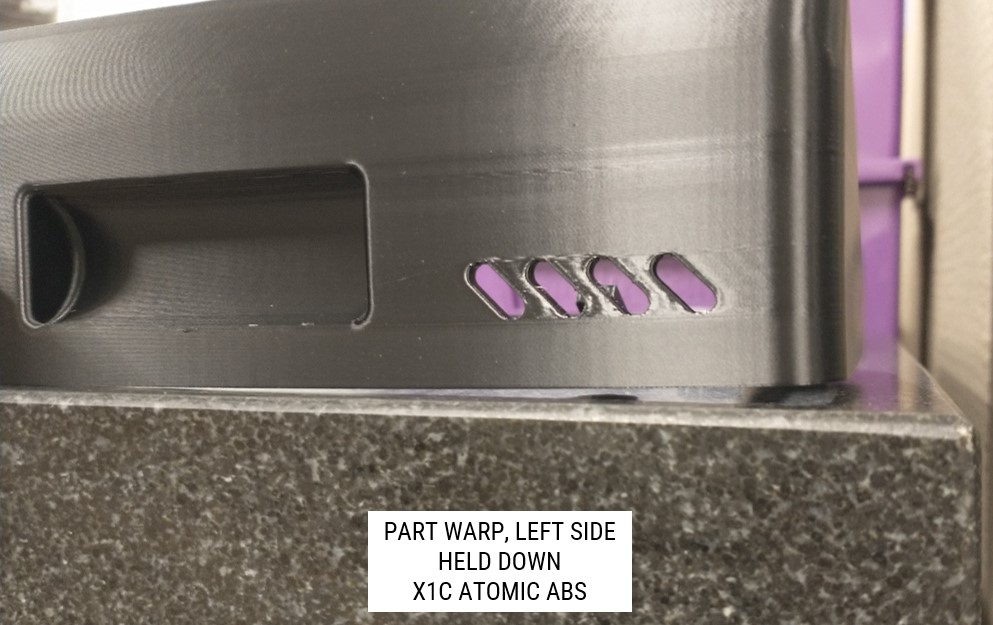
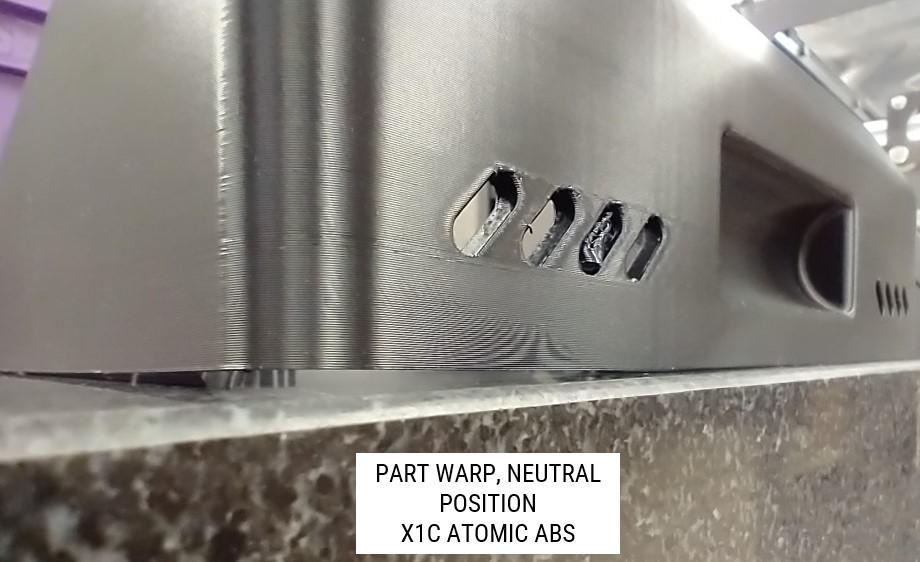
Case Study 2: Attempt to Print Ultimachine PC
As part of our tensile and thermal testing, we attempted to print Ultimachine PC on the X1C to create a set of tensile test pucks.
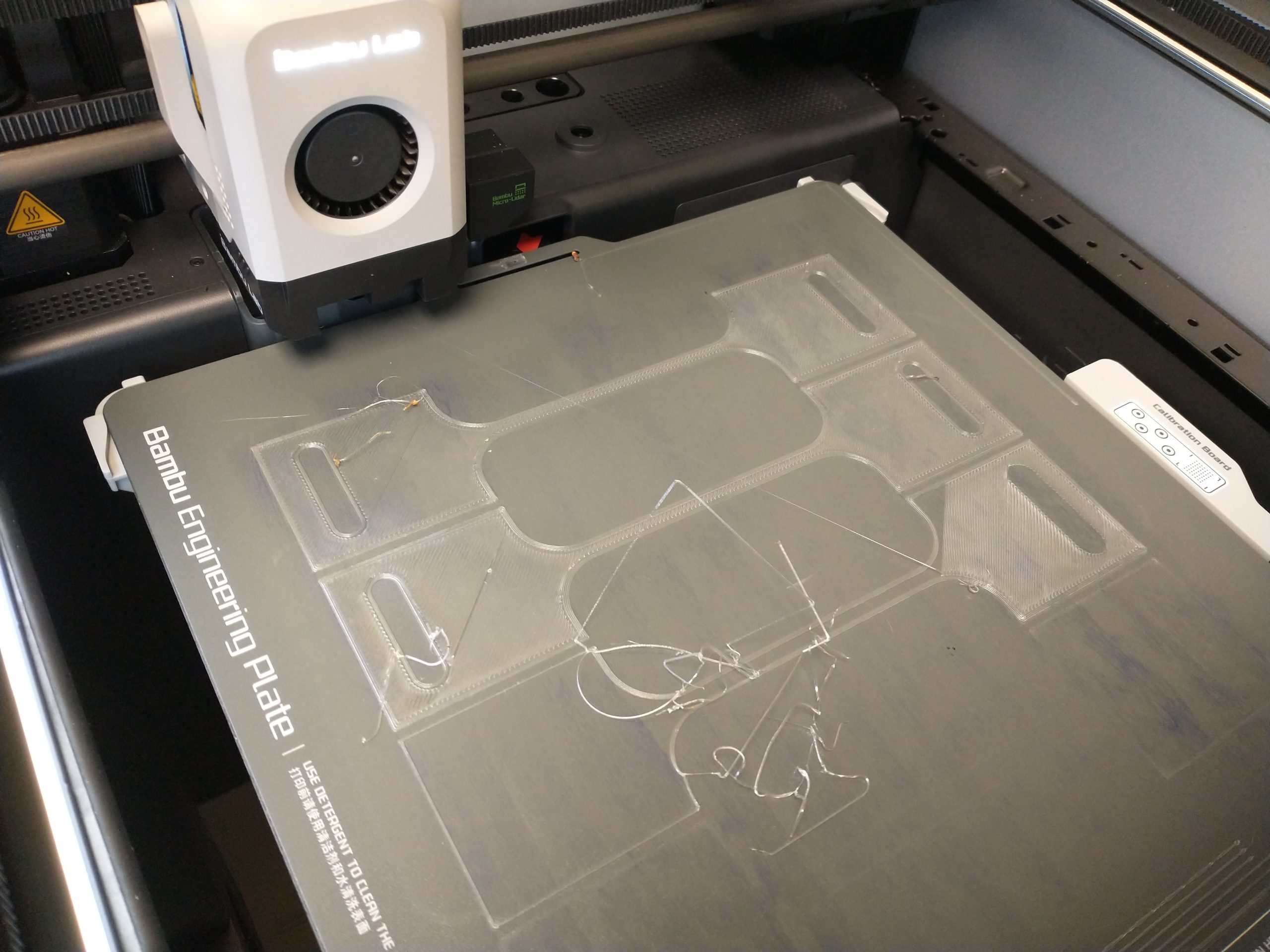
Specifications:
- Profile Used: Bambu Studio generic PC defaults
- Print Surface: Bambu Engineering Plate with purple glue stick coating.
The printer failed to complete the first layer of the print. The material either didn’t extrude from the nozzle or extruded briefly before stopping. Our team attempted the process two more times with the same outcome. Ultimatrely, the print head had to be replaced as it never printed PLA correctly again.
Published Data Doesn’t Tell the Full Story
In an ideal world, standardization testing such as Heat Deflection Testing (HTD) would tell users everything they need to know about their preferred materials. The reality, however, is that manufacturers can optimize materials for these tests to produce misleadingly favorable results.
The table below compares the specified HTD temperature with the temperature at wich deformation was first observed during our test:
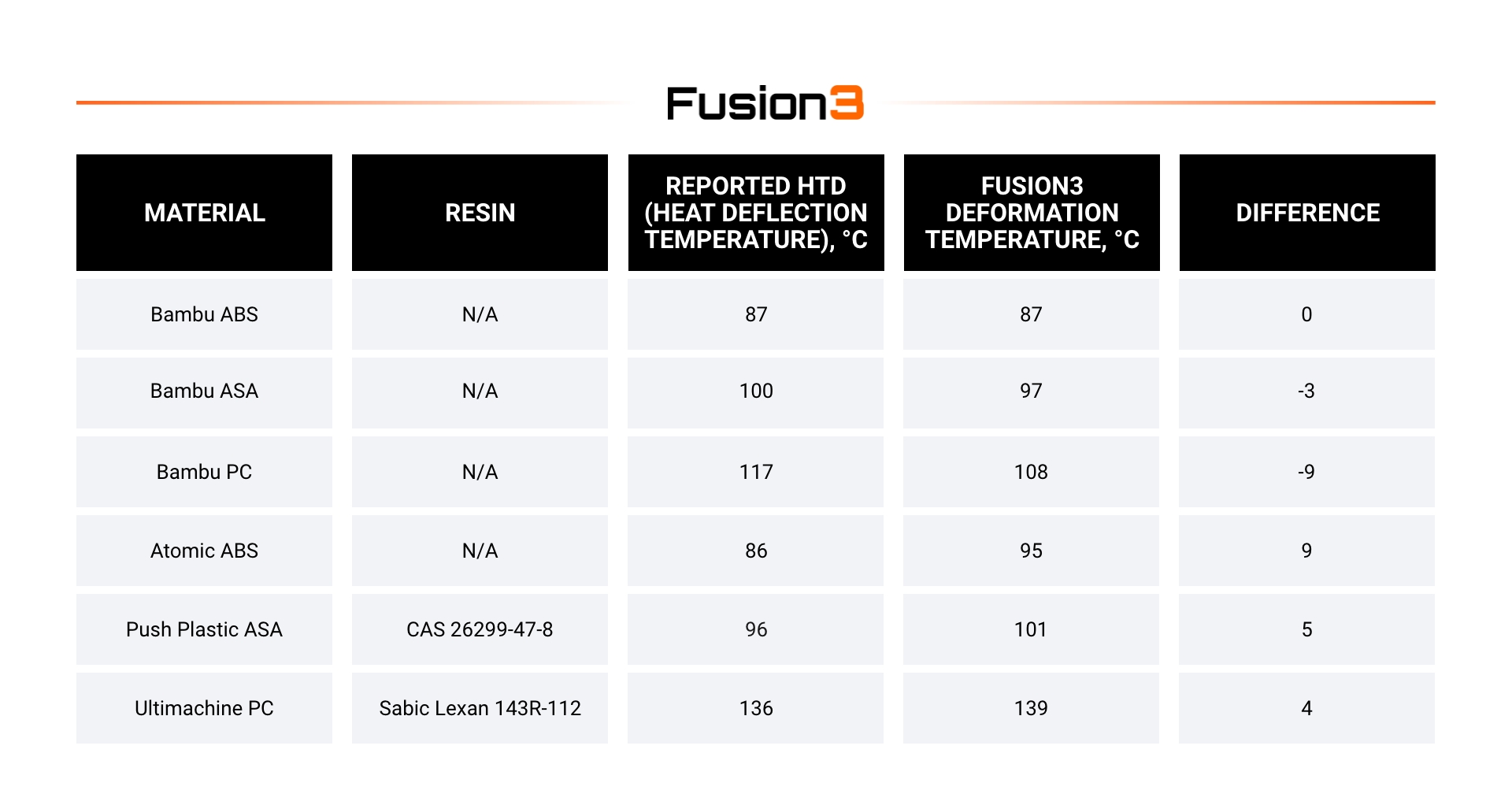